Sheet metal is a popular material used in various industries, including construction, automotive, and manufacturing. Cutting sheet metal is an essential task in these industries but can also be challenging. The process requires precision and expertise to avoid damaging the material and ensure the final product meets the desired specifications. However, cutting sheet metal work can be straightforward with the right tools and techniques. This article will discuss the easiest ways to cut sheet metal work, from selecting the right tools to implementing proper safety precautions.
Section 1: Tools for cutting sheet metal
There are various tools to choose from when cutting sheet metal work. Here are the most common tools used for cutting sheet metal:
Hand snips: Hand snips are the most basic and affordable tool for cutting sheet metal. They come in three types: straight-cutting, left-cutting, and right-cutting. They work by using a scissor-like action to cut through the metal.
- Pros: Hand snips are affordable and portable, making them an excellent choice for small projects.
- Cons: Hand snips are inaccurate and can be challenging for long periods.
Power shears are electric or pneumatic tools that use a blade to cut through metal sheets. They can make straight or curved cuts.
- Pros: Power shears are faster and more accurate than hand snips and can handle thicker metal sheets.
- Cons: Power shears can be expensive and require an external power source.
Plasma cutters: Plasma cutters use a high-temperature plasma arc to cut through metal. They are commonly used in industrial settings.
- Pros: Plasma cutters are fast and accurate and can cut through thick metal.
- Cons: Plasma cutters are expensive and dangerous if not used properly.
Laser cutters: Laser cutters use a laser beam to cut through sheet metal. They are commonly used in manufacturing and fabrication.
- Pros: Laser cutters are highly accurate and easily cut through thick metal.
- Cons: Laser cutters are expensive and require an external power source.
When choosing a tool for cutting sheet metal, consider the thickness of the material, the desired accuracy, and the available budget. Using the proper tool for the job is essential to avoid damaging the metal or injuring yourself.
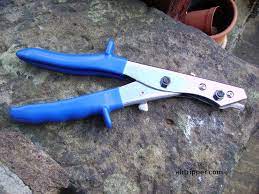
Section 2: Preparation for cutting sheet metal
Before cutting sheet metalwork, preparing the material properly is crucial to ensure a clean and accurate cut. Here are some tips for preparing sheet metal for cutting:
- Mark the cut line: Use a scribe or a marker pen to mark the cut line on the sheet metal. This will help you cut the metal accurately and avoid mistakes.
- Protect the surface: Use masking tape or a sacrificial piece of metal to protect the surface of the sheet metal from scratches and damage during the cutting process.
- Secure the sheet metal: Use clamps or a vice to hold the sheet metal securely in place during cutting. This will prevent the metal from moving or vibrating, which can affect the accuracy of the cut.
- Choose the right blade: Select the appropriate blade for your cutting tool based on the thickness and type of sheet metal. Using the correct blade can result in better-quality cuts or damage to the material.
- Wear protective gear: Wear appropriate protective gear such as gloves, eye protection, and hearing protection to avoid injury from metal chips or flying debris.
By adequately preparing the sheet metal, you can ensure a clean and accurate cut and prevent damage to the material or injury to yourself.
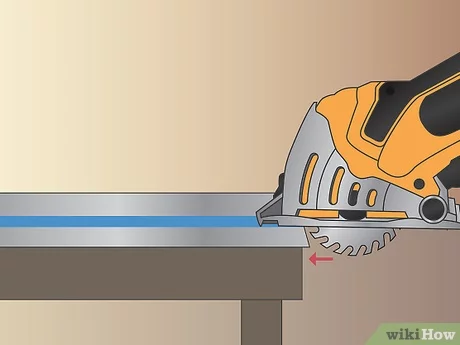
Section 3: Cutting techniques
There are several cutting techniques that you can use to cut sheet metalwork. Here are the most common techniques:
- Straight cutting: Straight cutting is the most basic technique for cutting sheet metal. It involves cutting the metal in a straight line using a tool such as hand snips or power shears.
- Curved cutting: Curved cutting involves cutting the metal in a curved or circular shape. This technique is often used in metalworking and fabrication.
- Complex shape cutting: Complex shape cutting involves cutting the metal into intricate or complex shapes, such as letters or designs. This technique is commonly used in artistic or decorative metalwork.
Here are some tips for cutting sheet metal:
- Use the proper technique for the type of cut you need to make.
- Move the cutting tool slowly and steadily to ensure a clean and accurate cut.
- Support the sheet metal adequately during cutting to prevent it from bending or vibrating.
- Take breaks if necessary to prevent the cutting tool from overheating.
- Use the appropriate cutting fluid if necessary to prevent overheating & extend the life of the cutting tool.
- Test the cut on scrap metal before cutting the piece to ensure accuracy.
You can ensure clean and accurate sheet metalwork by using the appropriate cutting technique and taking proper precautions.
Section 4: Safety precautions
Cutting sheet metalwork can be hazardous, and taking proper safety precautions to prevent injury is essential. Here are a few safety tips to keep in mind:
- Wear protective gear: Always wear appropriate protective gear such as gloves, eye protection, and hearing protection to prevent injury from metal chips or flying debris.
- Use the proper tool for the job: Use the appropriate cutting tool for the thickness and type of sheet metal you are cutting. Using the wrong tool can result in damage to the metal or injury to yourself.
- Keep your workspace clean & organized: A clean & organized workspace can help prevent accidents and injuries.
- Secure the sheet metal: Use clamps or a vice to hold the sheet metal securely in place during cutting. This will prevent the metal from moving or vibrating, which can affect the accuracy of the cut.
- Avoid cutting near electrical or flammable materials: Sparks and heat generated during cutting can ignite flammable materials or cause electrical shock.
- Turn off the cutting tool when not in use: Always turn off the cutting tool and unplug it when not in use to prevent accidental starts.
These safety precautions can prevent accidents and injuries and ensure a safe and successful cutting process.
How SJC Precision uses proper tools and techniques for cutting sheet metal
SJC Precision is a company that specializes in sheet metal fabrication and uses a variety of tools and techniques to ensure high-quality cuts. Here are some examples of how SJC Precision uses proper tools and techniques for cutting sheet metal:
- Laser cutting: SJC Precision uses laser cutting technology to produce clean, precise cuts in sheet metal. This technology is ideal for cutting complex shapes and intricate designs.
- Waterjet cutting: SJC Precision also uses waterjet cutting to produce accurate and precise cuts in sheet metal. This technique is ideal for cutting thicker materials and produces minimal heat and distortion.
- CNC machining: SJC Precision uses computer numerical control (CNC) machines to produce accurate and repeatable cuts in sheet metal. This technology allows precise control over cutting speed and depth, resulting in consistent quality cuts.
- Proper blade selection: SJC Precision selects the appropriate blade for each cutting job based on the thickness and type of sheet metal cut. Using the correct blade ensures a clean and accurate cut and prevents damage to the material.
- Preparing the sheet metal: Before cutting, SJC Precision prepares the sheet metal adequately, including marking the cut line, protecting the surface, and securing the metal with clamps or a vice.
By combining advanced technology and traditional cutting techniques, SJC Precision can produce high-quality cuts in sheet metalwork with precision and accuracy.