Sheet metal fabrication transforms flat metal sheets into a finished product through cutting, forming, and joining. Custom sheet metal fabrication is widely used in various industries, such as automotive, construction, electronics, and aerospace. This technique is essential to many manufacturing processes and can create everything from automobile parts to electronic enclosures. In this blog, we will see the best techniques for custom sheet metal fabrication, how to choose the proper technique for your needs, the typical applications of sheet fabrication, and the benefits of using this process.
Techniques for Sheet Metal Fabrication
Several techniques are used in custom sheet metal , each with benefits and limitations. Here are some of the most commonly used techniques for cutting, forming, and joining sheet metal.
Cutting Techniques
- Laser Cutting – A high-powered laser beam accurately cuts through the metal sheet. This technique suits various materials, including stainless steel, aluminum, and copper.
- Waterjet Cutting – A high-pressure stream of water mixed with abrasive particles cuts through the metal sheet. This technique is best suited for materials that are sensitive to high temperatures.
- Plasma Cutting – A high-temperature plasma torch melts through the metal sheet. This technique is suitable for cutting thicker sheets of metal quickly.
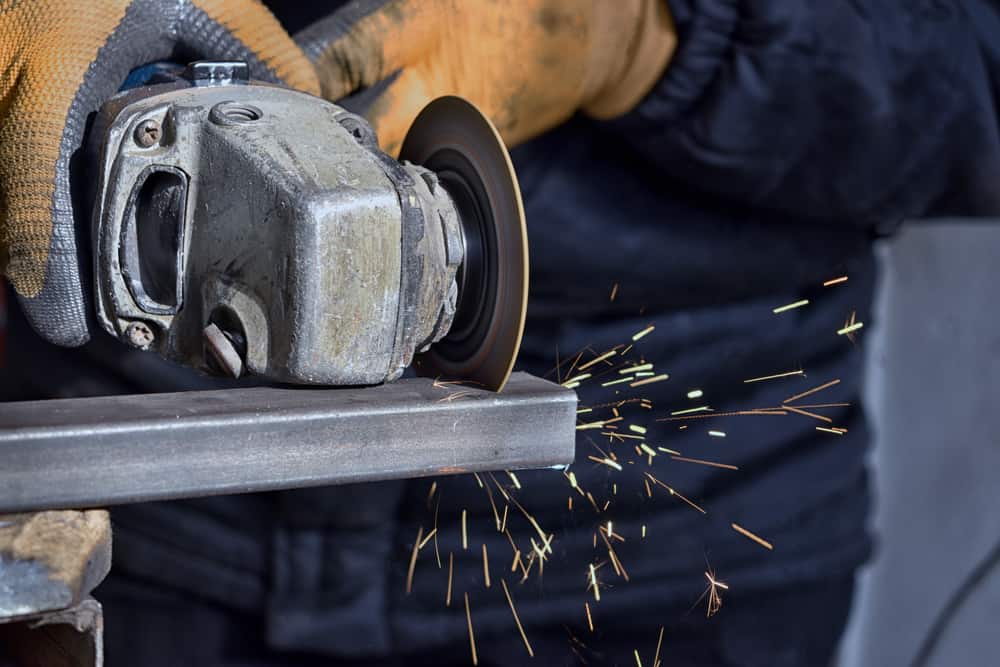
Forming Techniques
- Bending – The metal sheet is bent to a desired angle using a bending machine. This technique is commonly used to produce sheet metal parts with complex shapes.
- Rolling – The metal sheet is rolled into a cylinder shape using a rolling machine. This technique produces pipes, tubes, and other cylindrical structures.
- Stamping – The metal sheet is pressed into a desired shape using a stamping machine. This technique is commonly used to produce high-accuracy and precision metal parts.
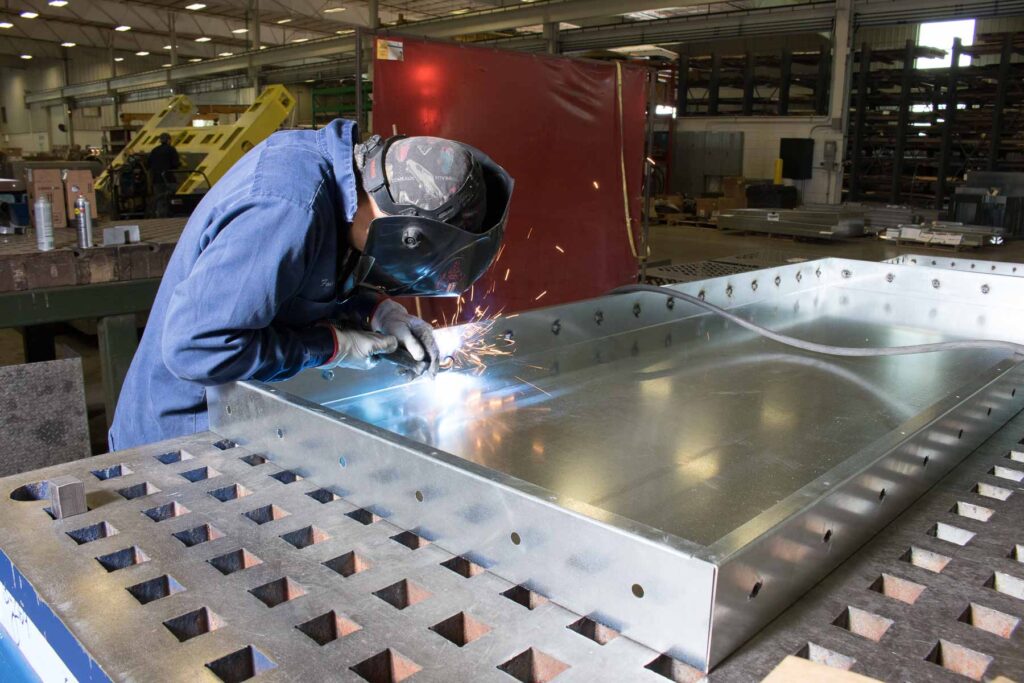
Joining Techniques
- Welding – Two or more metal sheets are joined together by melting, allowing them to cool and solidify. This technique is suitable for joining sheets of the same material.
- Riveting – A metal fastener joins two or more sheets of metal together. This technique is suitable for joining sheets of different materials.
- Adhesive bonding – A specialized adhesive joins two or more metal sheets together. This technique is suitable for joining sheets of different materials and provides a solid and durable bond.
Combining these cutting, forming, and joining techniques allows custom sheet metal fabrication to produce various parts and products.
Choosing the Right Technique
When choosing a custom sheet metal fabrication technique, there are several factors to consider, including material type, material thickness, precision requirements, and production volume. Here are some things to remember when selecting the proper technique for your needs.
- Material type – Different sheet metal materials require different cutting and joining techniques. For example, stainless steel may require laser cutting, while aluminum may be best cut with waterjet cutting.
- Material thickness – The thickness of the sheet metal also affects the choice of cutting technique. Laser cutting suits thinner sheets, while plasma cutting is better suited for thicker sheets.
- Precision requirements – Some applications require high levels of accuracy and precision, such as those in the electronics industry. Stamping and bending techniques can produce parts with high accuracy and repeatability.
- Production volume – The production volume of parts can affect the choice of cutting technique. For high-volume production, stamping and bending may be more efficient, while for low-volume production, laser or waterjet cutting may be more cost-effective.
- Considering these factors, you can choose the correct sheet metal fabrication technique for your application, producing high-quality parts and products.
Common Applications of Sheet Metal Fabrication
Sheet metal fabrication is used in various applications across different industries. Here are some common examples of where custom metal fabrication is used:
- Automotive Industry – metal fabrication is used to manufacture various parts of automobiles, including body panels, exhaust systems, and chassis components.
- Construction Industry – Sheet metal fabrication is used to manufacture HVAC (Heating, Ventilation, and Air Conditioning) systems, ductwork, and roofing materials.
- Electronics Industry – Sheet metal fabrication is used to manufacture enclosures, chassis, and brackets for electronic components.
- Aerospace Industry – Sheet metal fabrication is used to manufacture airplane, helicopter, and spacecraft components, including structural parts, engine components, and control surfaces.
Custom Sheet metal fabrication is a versatile technique that can be used to create complex structures & shapes. It is an essential component of many manufacturing processes, and its applications are limitless.
Benefits of Sheet Metal Fabrication
Sheet metal fabrication offers several benefits over other manufacturing techniques. Here are some of the critical advantages of using custom sheet metal fabrication:
- Cost-effectiveness – Sheet metal fabrication is a cost-effective way of manufacturing parts and products compared to other techniques, such as casting or molding.
- Durability – Sheet metal is a strong and durable material that can withstand harsh environments, making it ideal for construction, automotive, and aerospace applications.
- Versatility – Sheet metal fabrication can produce various parts and products with different shapes and sizes, making them suitable for various industries and applications.
- High precision – Sheet metal fabrication techniques such as stamping and bending can produce parts with high accuracy and precision, making them ideal for applications in the electronics industry.
- Customization – Sheet metal fabrication can be easily customized to meet specific requirements and be modified to suit different applications.
In summary, sheet metal fabrication offers several benefits, making it a popular choice for many sectors. Its cost-effectiveness, versatility, and durability make it an attractive option for various applications.
If you’re interested in custom sheet metal fabrication or have any questions about our services, please don’t hesitate to contact us at SJC Precision. You can reach us by email at info@sjcprecision.com or by phone at +1 (408) 262-1680. Our experts are always ready to serve you with your sheet metal fabrication needs.
To learn more about our services, visit our website at www.sjcprecision.com and see examples of our past work. We look forward to hearing from you!