In the field of sheet metal fabrication, CNC (computer numerical control) machines are becoming an increasingly popular method for creating precise and accurate final products. CNC machines In this blog, we’ll look into the various kinds of CNC machines used by sheet metal fabricators in more detail, along with the benefits they provide over standard approaches and the expertise needed to run and maintain them.
We will also explore how CNC machines are changing the way sheet metal fabrication is done and the future outlook for this technology in this field. Whether you’re a sheet metal fabricator, a designer, or an engineer, this blog will give you a deeper understanding of how CNC machines are revolutionizing the field of sheet metal fabrication.
CNC (computer numerical control) machines in sheet metal fabrication are becoming an increasingly popular method for creating precise and accurate final products. These machines use computer programs to control the sheet metal cutting, bending, and shaping, allowing for greater precision and accuracy in the final product.
Types of CNC Machine
Several different types of CNC machines are commonly used in sheet metal fabrication, each designed for specific types of fabrication. Some of the most popular types of CNC machines include:
CNC Laser Cutters: These machines use a high-powered laser beam to cut through the metal, making them ideal for cutting intricate shapes and designs. They are typically used for thin sheet metal and can cut through various materials, including steel, aluminum, and stainless steel.
CNC Punch Presses: These machines use a series of punches to create holes and shapes in the metal. They are typically used for making holes and other simple shapes in thicker metal sheets.
CNC routers: These machines use a rotating cutting tool to cut and shape the metal. They are typically used for cutting and shaping larger pieces of metal and can be used to create complex shapes and designs.
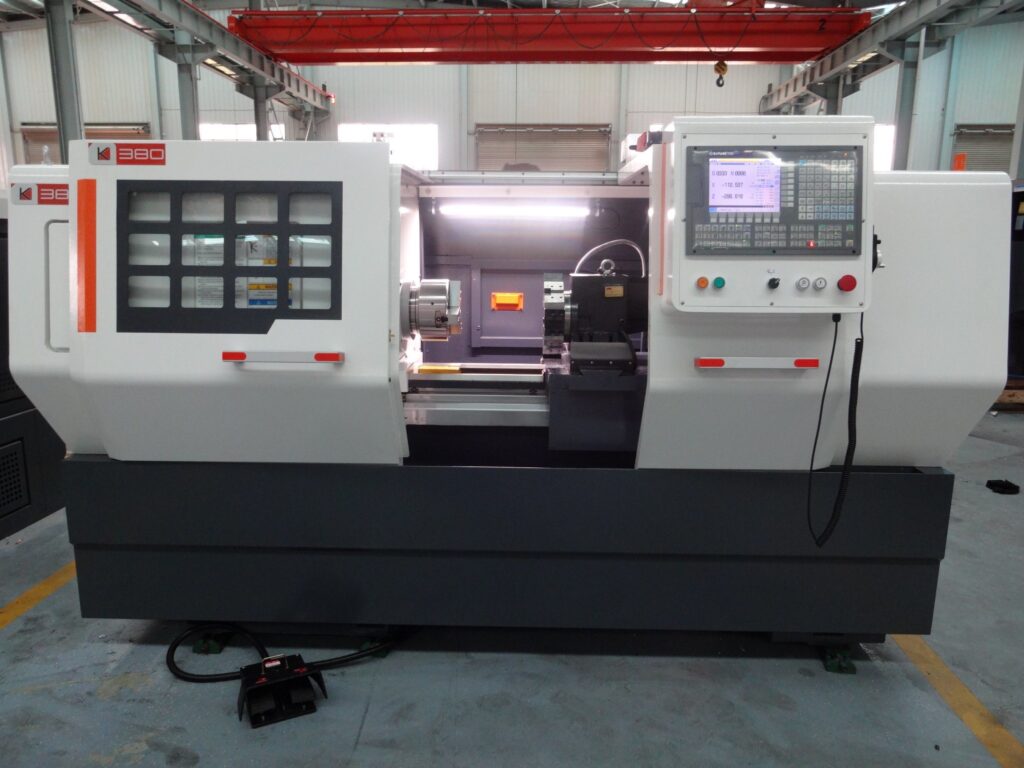
CNC Water Jets: These machines use a high-pressure stream of water to cut through the metal. They are typically used for cutting thicker metal sheets and can be used to create intricate designs and shapes.
Each of these machines has its unique capabilities and limitations, so it’s essential to choose the right one for the specific job.
Advantages of Using CNC Machines in Metal Fabrication
The use of CNC machines in sheet metal fabrication offers several advantages over traditional methods. For one, it allows for greater precision and accuracy in the final product. The machines can be programmed to cut and shape the metal to exact specifications, reducing the potential for human error. Additionally, CNC machines can work faster and more efficiently than traditional methods, leading to increased productivity and cost savings.
CNC machines also offer flexibility in fabrication. Once a program is written for a specific design, the machine can quickly produce multiple copies. This allows for the efficient and consistent production of identical products.
CNC Machines Over Traditional Methods
There are several advantages of using CNC machines over traditional sheet metal fabrication methods. Some of the most significant benefits include the following:
Increased precision and accuracy: CNC machines can cut, bend and shape the metal to exact specifications, reducing the potential for human error. This leads to a higher quality final product.
Greater efficiency: CNC machines can work faster and more efficiently than traditional methods. This leads to increased productivity and cost savings.
Flexibility in fabrication: Once a program is written for a specific design, the machine can quickly produce multiple copies. This allows for the efficient and consistent production of identical products.
Repeatability: CNC machines can produce the same part repeatedly with consistent precision, which is helpful in mass production.
Reduced labor cost: CNC machines can operate without human intervention, which reduces labor costs and increases productivity.
Versatility: CNC machines can handle different materials and thicknesses and create various shapes and designs.
Better Quality Control: CNC machines are equipped with sensors and monitoring systems, allowing for real-time quality control and adjustments during production.
Increased safety: CNC machines can perform dangerous or physically demanding tasks, reducing the risk of injury for the sheet metal fabricator.
CNC machines offer several advantages over traditional sheet metal fabrication methods, including increased precision and accuracy, greater efficiency, flexibility in fabrication, repeatability, reduced labor cost, versatility, better quality control, and increased safety. As technology continues to advance, the use of CNC machines will likely become even more prevalent in the sheet metal fabrication industry.
However, using CNC machines also requires high technical knowledge and skill. The sheet metal fabricator must be able to program and operate the machine, troubleshoot any issues that arise, and make necessary adjustments to the program as needed.
In conclusion, using CNC machines in sheet metal fabrication is becoming increasingly popular for creating precise and accurate final products. From CNC laser cutters to CNC punch presses, routers, and water jets, there are a variety of CNC machines available to sheet metal fabricators, each with its pros and cons. These machines offer several advantages over traditional methods, including increased precision and accuracy, greater productivity, cost savings, and flexibility in fabrication.
However, using CNC machines also requires a high level of technical knowledge and skill from the sheet metal fabricator. As technology advances, CNC machines in sheet metal fabrication will likely become even more prevalent, and sheet metal fabricators need to stay updated with new technologies and advancements in the field to remain competitive in the industry.