Precision metal fabrication is a critical process in the manufacturing business that involves precisely shaping, cutting, and assembling metal components. This method is used to make various goods in various industries, including aerospace, automotive, electronics, medical, and defense. Precision metal fabrication necessitates using advanced technology, expert personnel, and specific materials to produce components that satisfy the highest quality and performance criteria.
This blog will look at the processes, materials, applications, benefits, and challenges of precision metal manufacturing. We will also look at the field’s possibilities and provide recommendations for manufacturers and consumers. At the end of this blog, you will better know how precision metal fabrication plays a vital part in modern production and how it can assist various industries.
Methods for precision metal fabrication
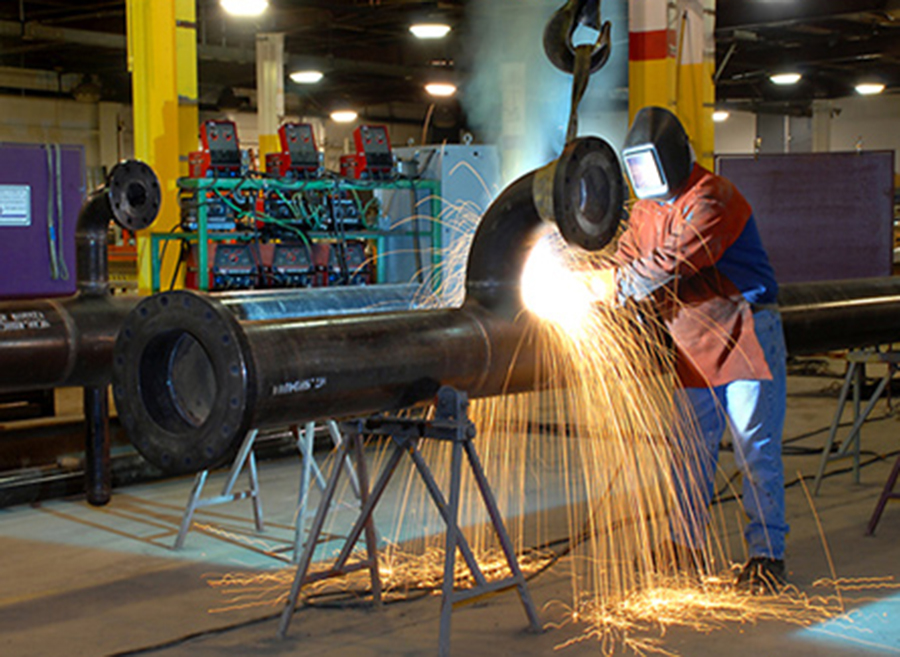
Many techniques are used in precision metal production to accurately and precisely shape, cut, and assemble metal components. Following are a few of the methods used most frequently in the manufacturing of precision metal:
A. Cutting: Accurate cutting can be accomplished using a variety of techniques, and it is a crucial step in the precision metal fabrication process. Some of the most popular ways to cut include:
- Laser cutting: A laser beam that is highly focused is used to cut through metal precisely. This technique can make thin metal sheets into complicated forms and patterns.
- Waterjet cutting: To cut through metal, a high-pressure jet of water combined with an abrasive substance is used. This approach is excellent for cutting thick metal sheets and may be applied to various materials.
- Plasma cutting involves melting metal with a high-temperature plasma arc. This technology is commonly used in the automotive and construction industries for cutting thick metal sheets.
B. Bending: Bending is the technique of shaping metal sheets or pipes into bends and curves. Accurate bends can be achieved using a variety of techniques, including:
- Press brake bending: Using a press brake machine to exert pressure on metal sheets, press brake bending produces exact bends at predetermined angles.
- Roll bending: Roll bending involves bending metal sheets or pipes into a specified form or curve using a group of rollers.
C. Welding: Welding is welding two or more metal components using heat or pressure. Precision metal fabrication employs a variety of welding techniques, including:
- TIG welding: TIG welding creates a high-temperature arc using a tungsten electrode, which melts the metal components together. This technique is excellent for producing accurate, high-quality welds.
- Metal inert gas (MIG) welding: MIG welding creates a high-temperature arc using a wire electrode, melting the metal components. This technique is excellent for producing solid and efficient welds.
- Laser welding: A highly focused laser beam fuses metal components. This technique produces precise and high-quality welding in thin metal sheets.
D. Finishing: Adding a final layer to metal components to enhance their appearance or performance is known as finishing. In the manufacture of precision metals, a few typical finishing techniques are as follows:
- An electrostatically charged dry powder is used when coating metal components with powder. The finish is durable and appealing by baking the powder at a high temperature.
- Anodizing is the electrolytic process of coating metal parts with a layer of protective oxide. This treatment enhances the durability and corrosion resistance of the metal.
- Plating covers metal components with another metal, such as chrome or nickel. This procedure improves the metal’s beauty and corrosion resistance.
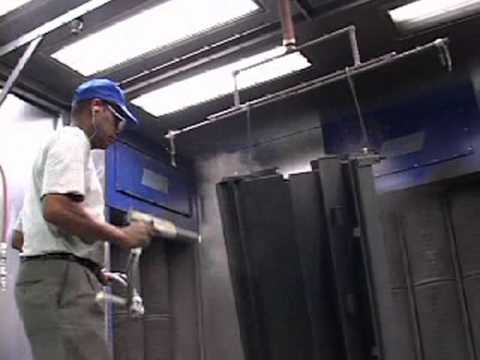
Applications for the precision metal fabrication
Several industries need precision metal production, including aerospace, automotive, electronics, medical, and defense. The following are a few of the most typical uses for precision metal fabrication:
- Aerospace: To produce strong, lightweight components for airplanes, satellites, and spacecraft, the aerospace industry significantly relies on precision metal fabrication. Components, including wings, fuselage, engine parts, landing gears, and control panels, are made with precision metal fabrication.
- Automotive: The production of components, including frames, chassis, engine parts, exhaust systems, and body panels in the automotive sector, uses precision metal fabrication. These components need to be extremely precise and accurate to ensure performance and safety.
- Electronics: Precision metal fabrication is used in the electronics industry to make components such as heat sinks, connections, and enclosures. These components require high accuracy and precision to ensure appropriate performance and endurance.
- Medical: In the medical industry, precision metal fabrication is utilized to make components such as surgical instruments, implants, and prostheses. To ensure safety and effectiveness, these components require high precision and accuracy.
- Defense: Precision metal fabrication is used in the defense industry to make components such as armored vehicles, weaponry, and military equipment. These components require exceptional precision and endurance to survive harsh temperatures and assure safety.
- Industrial: Various industrial applications, including manufacturing equipment, construction equipment, and agricultural machinery, employ precision metal fabrication. To guarantee efficiency and safety, these components must be exact and long-lasting.
Constraints in Precision metal fabrication
While there are numerous benefits to precision metal fabrication, there are also some difficulties that manufacturers must get through to produce high-quality metal parts. Some of the most typical difficulties in precision metal manufacturing are listed below:
A. Material selection: In precision metal production, selecting the best material for the particular application is essential. Various factors, including strength, flexibility, and corrosion resistance, influence the performance of various materials. The manufacturer must choose a suitable material that can survive the operational conditions and satisfies the demands of the consumer.
B. Design complexity: Precision metal fabrication frequently entails the creation of complicated forms and shapes that necessitate extreme accuracy and precision. These designs require advanced technology and competent personnel to ensure that the final product fulfills the specified criteria.
C. Cost: Precise metal manufacturing can be costly, mainly when intricate designs or specialist materials are used. Manufacturers must strike a compromise between production costs and the desired quality and performance of the finished product.
D. Quality control: To ensure the quality of precision metal fabrication, the components must be carefully inspected and tested. Manufacturers must have robust quality control methods to detect and fix any flaws or deviations from the specified specifications.
E. Safety: Precise metal fabrication requires heavy machinery, high temperatures, and potentially dangerous compounds such as chemicals and gases. Manufacturers must implement suitable safety protocols to safeguard their employees’ safety and prevent accidents.
F. Environmental impact: Using hazardous materials or creating trash during precision metal fabrication can significantly affect the environment. Manufacturers must implement sustainable practices to reduce their environmental impact and adhere to rules.
To find more information regarding our services and capabilities, visit our website at www.sjcprecision.com. We’re eager to talk with you and learn how we can help with your demands for precision metal fabrication.