I. Introduction to Tool & Die Making
Tool & die making is the process of designing, manufacturing, and repairing metal dies, molds, and cutting tools used in manufacturing industries. Tool & die making plays a critical role in the manufacturing industry as it ensures the production of high-quality, precise, and consistent products.
This blog aims to comprehensively understand tool and die making, including its history, process, tools, skills, and role in modern manufacturing (tool and die, maker). It will also provide valuable insights into the future of the industry of tool and die makers, and its potential challenges and opportunities.
II. The History of Tool & Die Making
- Evolution: Tool & Die Making has a rich history dating back to the medieval era when blacksmiths crafted simple tools and weapons. As manufacturing evolved, so did tool and die makers, with technological advances leading to the creation of more complex and precise tools.
- Key Innovations: Some critical innovations in Tool & Die Making include the development of machine tools, computer-aided design (CAD) software, and advanced materials and fabrication methods. These advancements have revolutionized the tool and die maker industry and made it possible to produce high-quality, precise, and efficient tools cost-effectively.
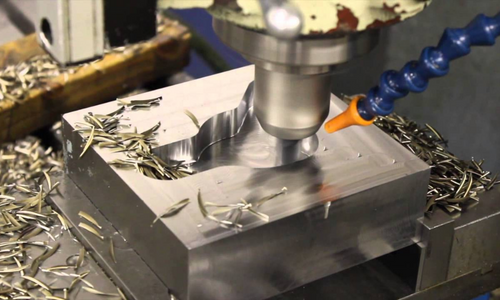
III. Understanding the Tool & Die-Making Process
- Steps: The Tool & Die Making process involves several steps, including design and planning, material selection, fabrication, heat treatment, finishing, and testing.
- Types of Tools & Dies: There are various tools and dies used by tool and die, makers, including cutting tools, molds, dies for forging and stamping, and jigs and fixtures.
- Design Considerations: When designing tools and dies, different factors need to be considered, including the material to be used, the manufacturing process, the required tolerances, and the desired lifespan of the tool. A thorough understanding of the manufacturing process and the properties of different materials is crucial in designing efficient and effective tools and dies.
IV. Essential Tools & Equipment in Tool & Die Making
A. Power Tools: Power tools, such as drill presses, milling machines, and grinders, are used to shape and finish metal.
B. Precision Measuring Tools: Precision measuring tools, such as micrometers and calipers, ensure accurate measurements and high-quality results.
C. Machine Tools: Machine tools, such as lathes and EDMs, fabricate and shape metal components.
D. Hand Tools: Hand tools, such as chisels and files, are used to perform fine-tuning and finishing work.
It’s important to note that the tools and equipment used in Tool & Die Making are specialized and require proper training and safety measures to operate effectively.
V. Skills & Training for Tool & Die Makers
- A.Technical Skills: Tool and Die makers must understand metal properties, manufacturing processes, and engineering principles strongly. Tool and Die makers also need to be proficient in using specialized tools and equipment.
- B.Soft Skills: Besides technical skills, Tool, and Die Maker must have excellent problem-solving skills, attention to detail, and the ability to work independently and in a team environment.
- C. Training & Certification: Tool and Die makers typically receive training through apprenticeships, on-the-job experience, and technical schools. Certification programs are also available to demonstrate expertise and proficiency in the field. It’s essential for Tool & Die Makers to continuously update their skills and knowledge to stay current in an ever-evolving industry.
VI. Tool & Die Making in the Modern Manufacturing Industry
- Advances in Technology & Automation: Technology and automation have transformed the Tool & Die Making industry, making it possible to produce high-quality tools and dies more efficiently and cost-effectively.
- Challenges & Opportunities: Despite the advancements, the industry faces several challenges, such as the need to adapt continuously to new technologies and the increasing demand for highly specialized skills. However, the industry also presents several opportunities, including the growing demand for precision manufacturing, the development of new materials, and the increasing use of automation in the production process.
- The Future of Tool & Die Making: The future of Tool & Die Making is bright, with continued advancements in technology and automation expected to drive the industry forward. The increasing demand for precision manufacturing and the need for highly specialized skills will allow the industry to grow and thrive.
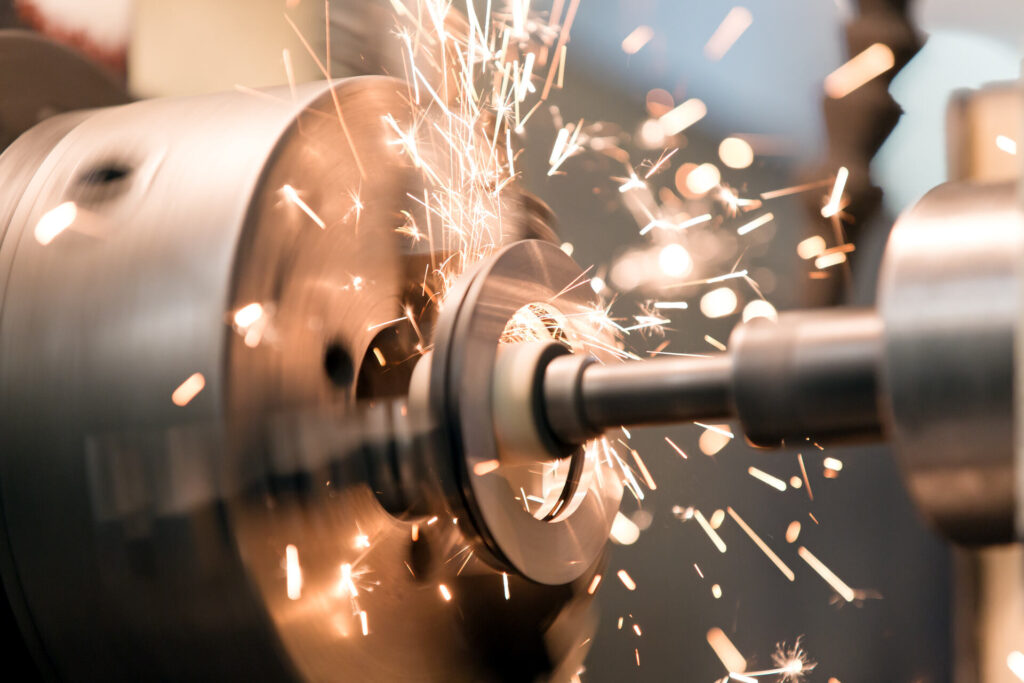
How SJC Precision helps your business in Tool & Die making
- Expertise & Experience: SJC Precision has a team of experienced Tool and Die makers with a deep understanding of the industry and a commitment to providing high-quality, precise, and efficient solutions.
- Advanced Technology & Equipment: SJC Precision invests in advanced technology and equipment, allowing them to stay at the forefront of the business and provide cutting-edge solutions to their clients.
- Customized Solutions: SJC Precision understands that every business has unique requirements and offers customized solutions to meet its client’s specific needs.
- Commitment to Quality: SJC Precision is dedicated to delivering high-quality results. Their commitment to quality is evident in every aspect of their work, from design to fabrication.
- Support & Service: SJC Precision provides comprehensive support and service, ensuring their clients have the resources and assistance they need to succeed.
By partnering with SJC Precision, businesses can take advantage of their expertise, advanced technology, and commitment to quality to achieve their Tool & Die Making goals and succeed in the highly competitive manufacturing industry.